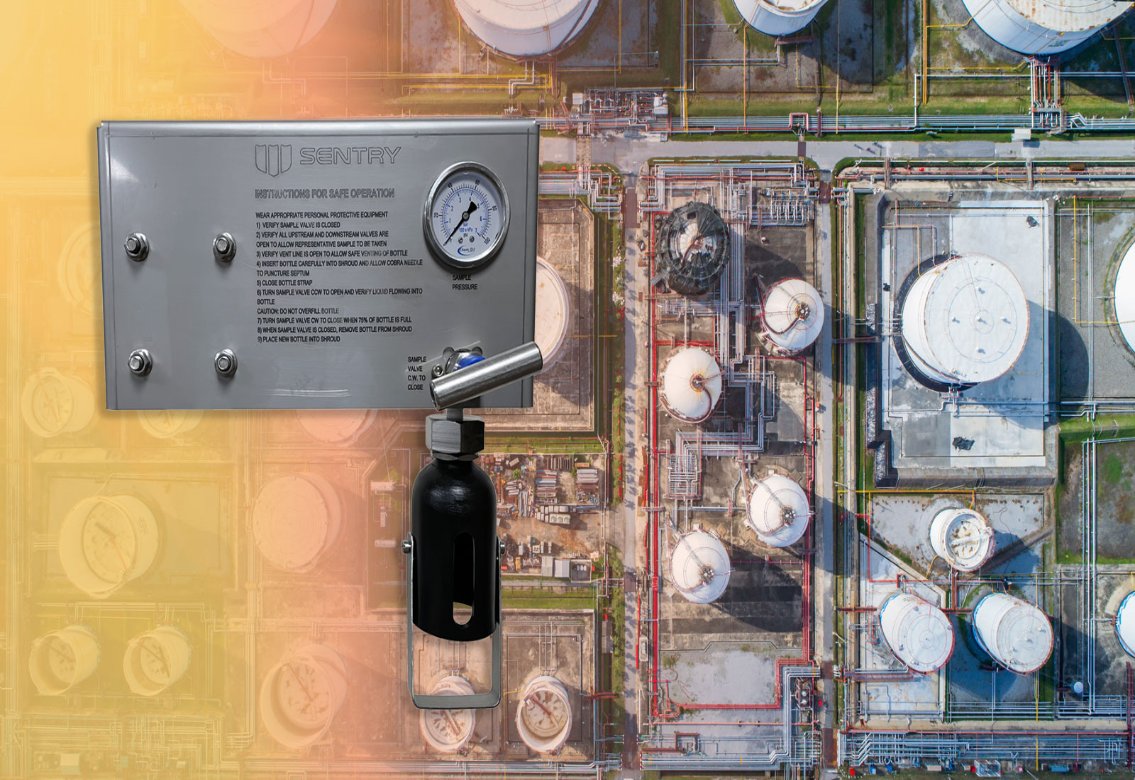
In the petrochemical and refinery industries, operations must run safely and efficiently with controlled, real-time data. Plants can eliminate data imprecision by transitioning to a low-emission (Low-E) closed-loop gas and liquid sampling system.
Low-e sampling, combined with proper staff training, can help maximize sampling accuracy while minimizing risks to people, equipment, and the environment.
The Shield sat down with Senior Service Manager Randy Cruse to discuss how oil and gas producers can use Low-E samplers to protect their products and people.
The Shield (TS): What are Low-E sampling systems?
Randy Cruse (RC): Low-e systems are simple, safe, and accurate ways to manage representative sampling in an oil and gas plant. They're designed to help plant operators pull fresh material directly from the process flow to deliver an accurate representative sample. They keep liquids and gases contained, and operators use a series of valves and vents to control the low e-sampling process.
TS: Why do plants choose the low-emission samplers over other sampling systems?
RC: Plants use Low-E samplers for several reasons, primarily safety, simplicity, and accuracy.
- Safety. The most important reason to choose Low-E samplers is to keep operators safe because they separate the process from the person. Low-e samplers also capture emissions and send them to a secure location, a vapor recovery, or a flare system.
- Simplicity. Operators don't have time to learn the intricacies of a multi-valve panel. Low emission panels are easy to use, with simplified systems that save a considerable amount of time.
- Accuracy. They ensure reliability, repeatability, and accuracy. Because they pull directly from the process flow, there's no guesswork as to age or potential detrimental exterior impact. Test results are consistent and reliable.
TS: How do plants know which Low-E sampler is best for their application?
RC: Choosing a Low-E sampling system comes down to three things: what we're sampling, the properties of that sample, and how the lab requests the sample.
We use Cobra HTHV samplers with a cabinet for heavy fluids with high viscosity to separate the operator from the sample since we will be required to use an open-top container. We'll use our Cobra SS or M samplers with a cap and septa and a vent system to reduce emissions and protect the operator from lighter liquids with low vapor pressure.
For liquid petroleum gases (LPG), we use a cylinder with our Cobra C sampler. Typically, they're brought to the lab in a liquid phase and then gassed off to Gas Chromatography systems (GCs) when they're analyzed. We also use a sight flow indicator to make sure that we're getting a liquid sample.
If it's a straight gas, we use that same sample station without a sight flow indicator. And we flow it from the top down to push out any condensate or other liquid in the gas.
Our website is beneficial for helping customers choose which Low-E sampler is suitable for them.
TS: What are the connections and process considerations before installing a sampling system?
RC: The most important consideration is location. We need a sampling point that includes the characteristics we're looking for in that fluid or process. Most crucially, we need to create a loop across a device that creates a pressure drop. Typically, a control valve is the best choice because we can find connections on both sides of the control valve. A continuous flow ensures we are able to obtain a representative sample.
TS: What are the maintenance requirements on low emission samplers?
RC: First and foremost, each operator should be trained to execute sampling effectively.
Preventive maintenance (PM) should also be put in place to ensure that equipment is always in working order.
A fixed volume liquid system includes monitoring and maintaining wear points on gauges. Pressure regulators need to be checked periodically to ensure they're in the usable range, as they tend to drift over time. Needles should be cleaned, polished, sharpened, or replaced. Main valves should be assessed for a bubble-tight shutoff.
With cylinder systems, quick-connects should be replaced at least every year. Stainless steel flexors also should be replaced every two years. Vent and sample valves should be checked often for damage, as should gauges.
TS: How can plants maximize results from their Low-E sampling program?
RC: Plants need to have well-trained, experienced personnel to operate and maintain these systems. A good partner with experience and a good track record is invaluable in this area.

Written by Sentry Equipment
With proven sampling expertise since 1924, Sentry products and services provide business operations the critical insights to optimize process control and product quality. We deliver true representative sampling and analysis techniques to customers around the globe, empowering them to accurately monitor and measure processes for improved production efficiency, output and safety. Standing behind our commitments, we are determined to tackle any application, anywhere.
Related Posts
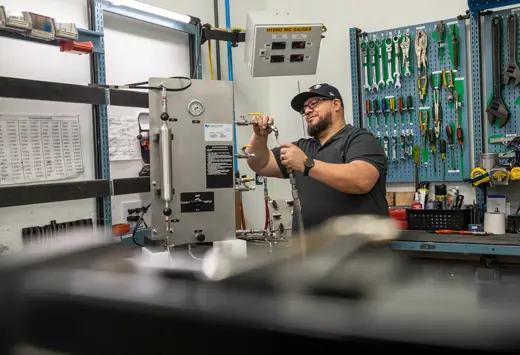
Mitigate Process Damage
Sentry's low-emission samplers helps protect your operation and employees from caustic materials.