Repair vs. Replace: Managing Your Refinery's Sampling Equipment
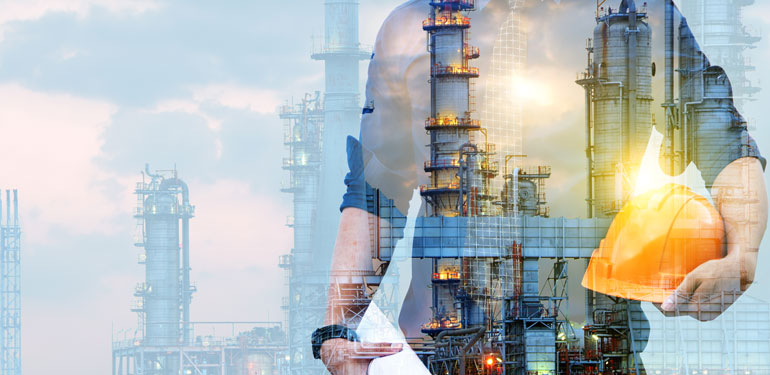
Within these plants, hydrocarbon sampling systems and equipment are often overlooked, even as new technology and regulations demand more from them.
With aging equipment and facilities, operators face increasing challenges in maintaining equipment’s reliability and integrity, as well as safety. One of the biggest hidden threats to your plant’s efficient and safe operation is deteriorating sampling equipment.
However, it can be difficult to know when to continue maintaining or repairing sampling equipment, and when to replace it.
SIGNS YOUR SAMPLING EQUIPMENT NEEDS ATTENTION
These are some of the signs you might encounter if your hydrocarbon sampling equipment needs to be repaired or replaced:
- Maintenance data is coming back with recurring issues
- Lab data is indicating sampling errors or contaminated samples
- Location and/or tie-in points no longer meet your sampling needs
- Systems aren’t installed in the right locations to execute your plant’s processes
- Changes have been made to the sample requirements (conditioning, quantity, etc.) or formula since equipment was installed
- New technology has been developed – improving method or components for safety, accuracy and/or reliability
- Equipment has been degraded due to corrosion, erosion, wear or fatigue
- Equipment is now obsolete and lacks spare parts
- Changes to regulations have occurred - such as new requirements in the Clean Air Act
These factors put a strain on aging sampling equipment, especially in the case of sensitive components like quick disconnects, regulators and check valves. These components, along with others, often result in unacceptable performance if not serviced regularly.
THE RIGHT MAINTENANCE OPTION FOR YOU
Choosing the right upgrade or replacement based on key considerations can give hydrocarbon plants a second life and help avoid downtime or even a devastating shutdown.
When deciding whether to hang on to a piece of equipment through regular maintenance or spend the funds to upgrade or replace it, asset managers must consider a number of factors, including:
- Cost of the repair, upgrade or replacement
- Age of the equipment
- Process condition exposure
- Harsh environmental condition exposure
- Expected life cycle with or without repairs/upgrade
Cost is often the biggest factor when considering upgrading or replacing hydrocarbon equipment. When assessing this major consideration, it is important to ask yourself:
- How much would it be to upgrade the equipment?
- How much to replace it altogether?
- How much would it be to retrofit the existing equipment with updated technology?
Understanding these questions can help determine how long equipment can operate to specifications before the cost of general maintenance and repair exceeds the cost of replacing the equipment.
MAKE IT EASIER TO REPAIR, UPGRADE OR REPLACE
- Keep good maintenance program records – These will help you track past incidents and repairs so you can determine if future repairs or replacement is a better decision.
- Stay up-to-date on industry trends and sampling methods – This will ensure your equipment is never obsolete and has the latest functionality to deliver the precise measurements you need.
- Maintain a strong sampling plan – Retrofits or replacements aren’t always necessary if you have a sampling plan that makes it easy to identify needs.
- Pay attention to your sampling systems – Sampling equipment and systems should be treated with the same importance as every other piece of equipment in the plant.
Whether you are repairing or upgrading your equipment, keeping your sampling equipment running with confidence is the goal. Don’t leave it to chance with equipment you can’t trust.
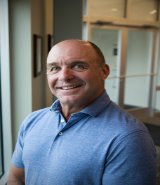
Written by Randy Cruse
As Senior Service Manager, Randy dedicates his lengthy career to developing and delivering service programs designed specifically for refineries and their sampling programs. He understands the risk and safety requirements that come along with being a service provider in the Oil & Gas industry and brings that expertise to each and every call.
Related Posts
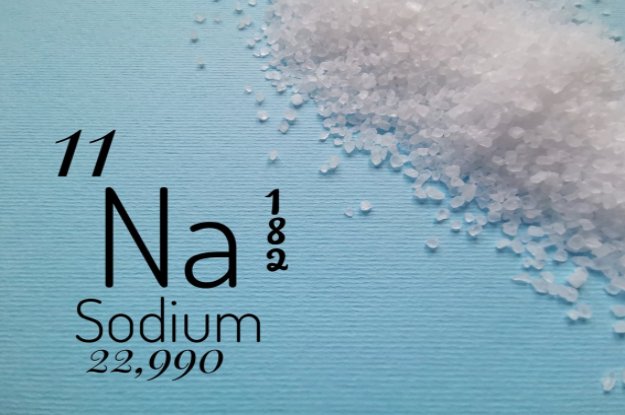
Preventative Maintenance
Monitoring Sodium in Power Plants
An increase in sodium measurements may identify unwanted dissolved impurities. When coated on the boiler turbine blades and heat exchanger surfaces, these impurities can cause catastrophic problems in power plants.
Read More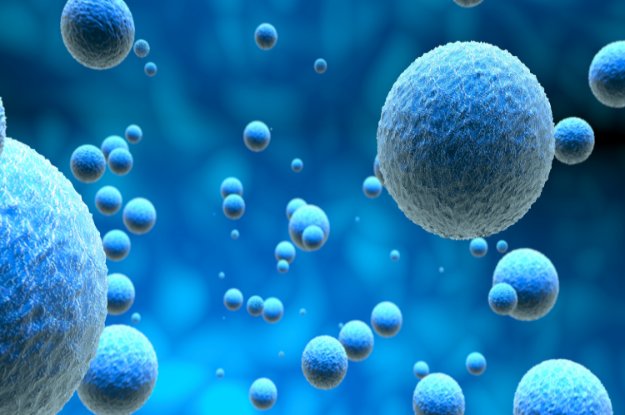
Preventative Maintenance
The Advantages of Chlorine Dosing to Control Biofilm in Industrial Cooling Systems
Microorganisms are organisms of microscopic size, which may exist in its single-celled form or as a colony of cells such as bacteria, fungi, and algae.
Read More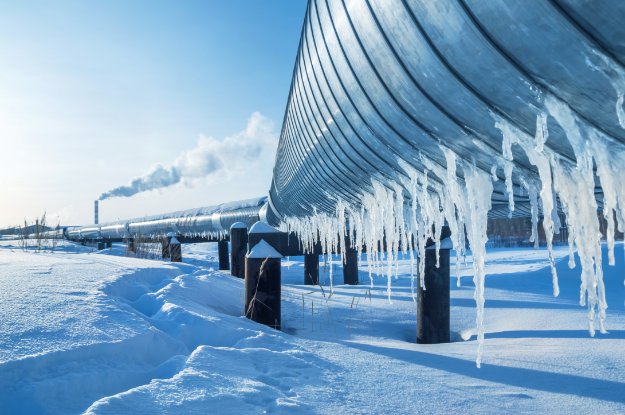
Preventative Maintenance
Avoid a Pipeline Freeze with a Methanol Injection Plan
As temperatures drop, equipments risk of damage increases.
Read More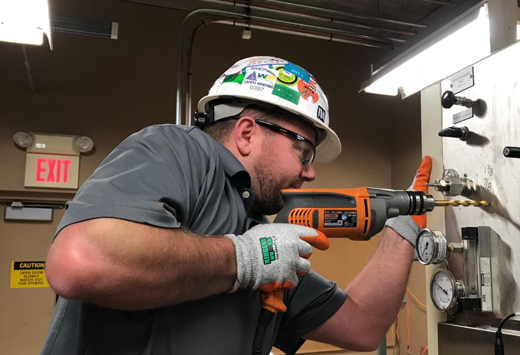
Get Your System Inspected
Our ProShield Service Team can help you assess your sampling needs with a SysRep report.