The Importance of Industrial Boiler Water Treatment
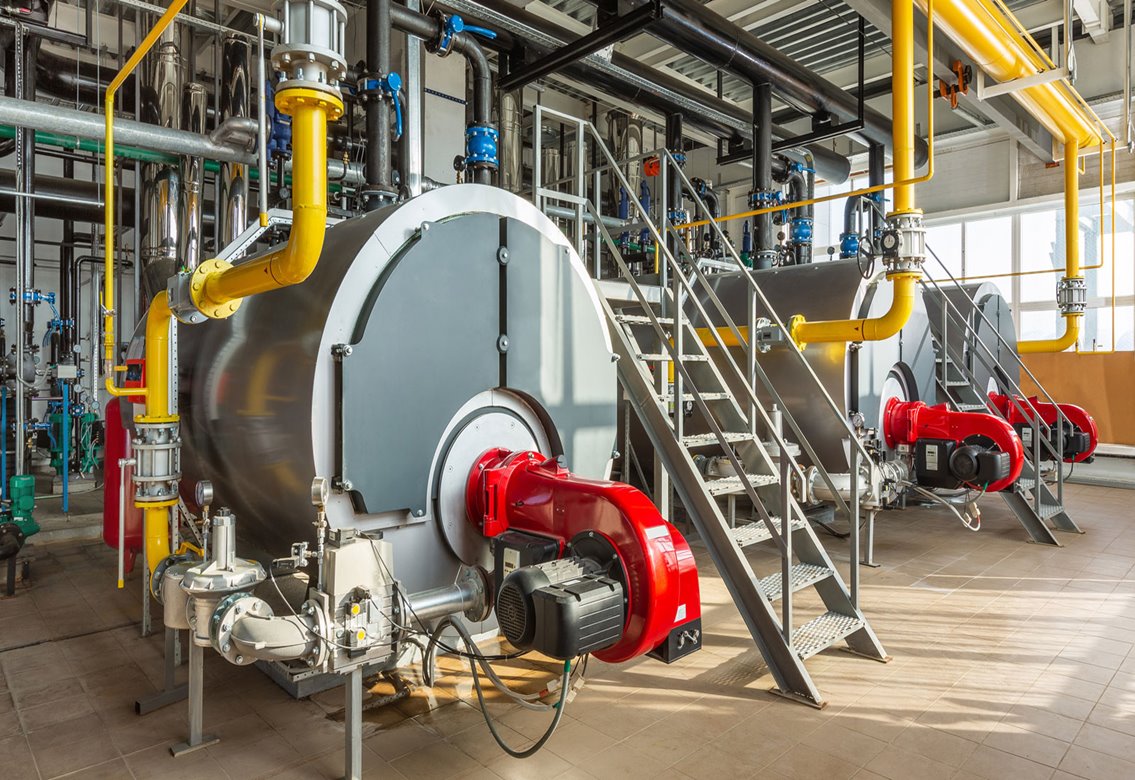
Industrial steam plants and combined steam and power facilities, also known as cogeneration plants, commonly use boilers to provide high-quality steam and electric power.
As the heart of the plant, these boilers are crucial to efficient energy creation. If impurities enter the boiler feedwater or corrosion develops inside the boiler, equipment can be damaged, the plant can experience unexpected downtime, and energy creation can be extremely ineffective. It’s critical to limit impurities and corrosion in a boiler system to maximize boiler output and prevent these challenges.
Boiler Corrosion and impurities can lead to failures
Many medium- to high-pressure boiler systems, including carbon steel boilers, suffer from corrosion and impurities.
Chemical treatment in industrial boilers can be complicated due to:
- Impurity ingress from steam feed and condensate return systems
- Impurities, such as hardness, from inadequate makeup water treatment system performance
- Condensate return system corrosion that damages piping and equipment, and sends iron oxide corrosion to the boiler, which can deposit and reduce effective heat transfer
Process steam carries heat from cogeneration plants. This steam delivers the latent heat to the manufacturing process, leaving liquid condensate. Theoretically, the condensate should be clean water. But in practice, the processing system introduces contaminants into the liquid stream and condensate return, including iron, copper, ammonia, magnesium, calcium and organic carbon.
All of these contaminants negatively affect the feedwater systems, boilers and turbines in the plant, potentially causing unnecessary downtime and equipment damage.
Condensate makeup is not required to be demineralized – which can cause buildup of these impurities in boilers. The introduction of water impurities to the boiler can lead to higher conductivity, increasing corrosion potential. In addition, heavy mineral deposits restrict heat transfer.
Manage Boiler Water with Cycle Chemistry
1. Chemical-reducing substances. A chemical-reducing agent can lower dissolved oxygen levels to prevent or minimize corrosion within the boiler and turbines. These materials include scavenger chemicals or corrosion inhibitors injected into the boiler or boiler feedwater. They’re often delivered via injection equipment, such as atomizers or sample quills.
For example, in steam generators that commonly operate at or below 600 psi, uncatalyzed or catalyzed sodium sulfite (Na2SO3) is a non-volatile oxygen scavenger that adds inorganic dissolved solids to the feedwater.
Additionally, corrosion and cooling/heating equipment can help maintain purified water with little contaminants from materials.
2. Film-forming substances (FFS). FFS are a range of corrosion-inhibiting products for boiler chemistry, including film-forming amines (FFAs).
FFS inhibit corrosion by forming a very thin, non-wetable film on the surface of power plant equipment, which acts as a barrier between the metal surface and the water/steam phase to help reduce corrosion. Organic cycle chemistry based on FFS is being increasingly employed as an alternative to conventional treatment programs because they inhibit corrosion while maintaining clean heat transfer surfaces.
3. Boiler water treatment. Industrial boiler water treatment helps protect low-pressure steam generators often found in co-generation plants. Boiler water can be treated with several agents, including a phosphate/polymer combination, polymers alone, and (rarely) chelating agents.
Trisodium phosphate (Na3PO4), also known as TSP, is a common boiler water conditioning chemical that establishes moderately alkaline conditions in the boiler to minimize corrosion and reduce scaling where hardness ingress occurs. Phosphate treatment programs use blends of tri- di- and monosodium phosphate for pH control as well.
It’s also recommended that sludge conditioners using water-soluble polymers can help keep solids in suspension by a combination of dispersion, crystal modification and sequestration, in addition to phosphate treatment. Sludge conditioners can also help keep iron particles in suspension for subsequent blowdown.
Chelants, such as ethylenediaminetetraacetic acid (EDTA), sometimes can be used to bind with metals to keep them suspended. However, chelants should be used only with well-deaerated feedwater, excellent pre-treatment control and low feedwater iron concentrations.
Choosing the appropriate treatment depends on a variety of factors, including boiler design and pressure, the effectiveness and reliability of the makeup water treatment system and the risk of impurity ingress and iron oxide carryover from condensate return. These factors must be evaluated carefully for each plant, as a standardized approach can lead to serious problems.
Once a treatment is chosen, monitoring chemistry Is the best way to ensure the treatment is working appropriately. A Steam and Water Analysis System (SWAS) comprised of properly selected sample conditioning equipment and on-line instrumentation is key to controlling and monitoring your system treatment regime.
Sentry can provide insight on the best solution for your plant, including SWAS and single line options. Contact us at +1-262-567-7256, or complete our online contact form for more information.
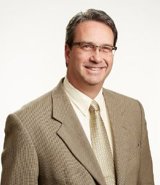
Written by John Powalisz
John Powalisz, Director of International Sales, is dedicated to sharing his technical expertise and knowledge of sampling equipment and systems in power plants, refineries, chemical and food processing facilities garnered from more than 19 years with the company. John has worked with clients worldwide to help them to comply with regulations and optimize processes by applying proper sampling hardware and techniques. While he is well-versed in all Sentry products and applications, he is particularly focused on the food and beverage and power generation markets as well as emerging market development.
Related Posts
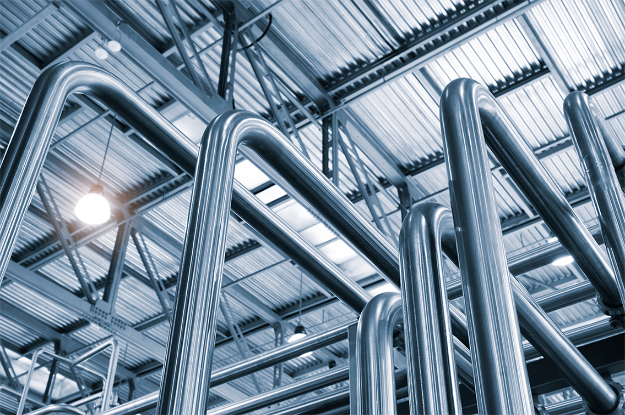
Power Generation
Do You Trust Your Process Analytics?
Accurate sampling all depends on regular maintenance. Are you maintaining the critical instruments that your plant relies on?
Read More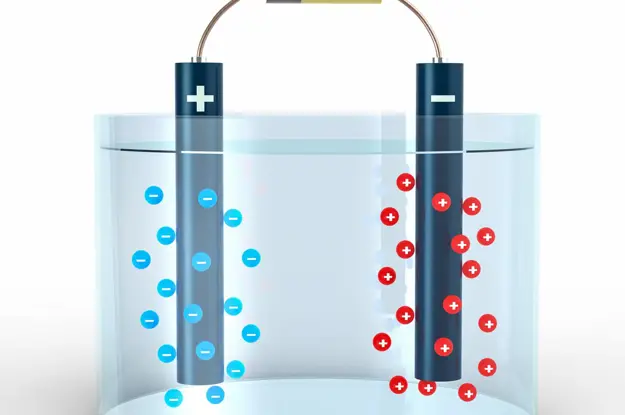
Power Generation
Cation Conductivity vs. Specific Conductivity
Conductivity is useful as a general measure of stream water quality. Each stream has a relatively constant range of conductivity. Once a baseline is established, it can be compared with regular conductivity measures.
Read More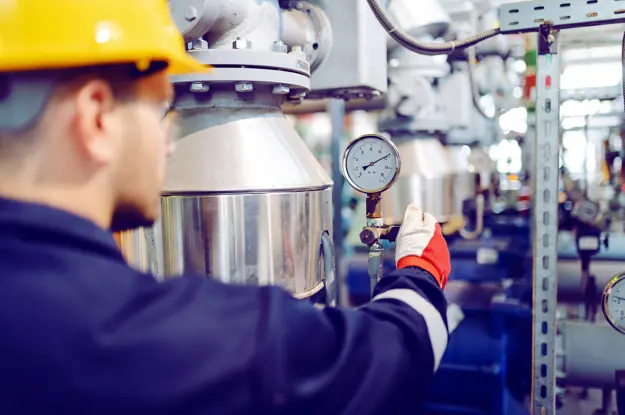
Power Generation
Monitoring Cooling Water Systems to Improve Plant Performance
Many plants within the manufacturing industry include processes where the product stream must be heated, cooled, or both to facilitate production. These plants often use heat exchangers or sample coolers with recirculating cooling water systems to do so.
Read More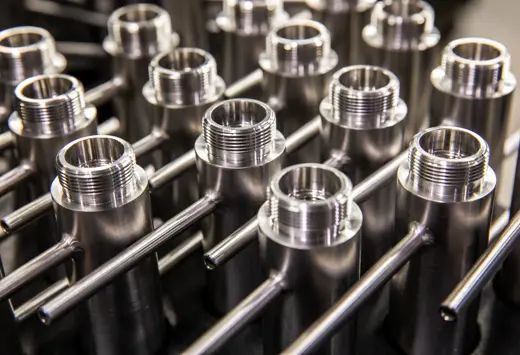
Protect Your SWAS
Sentry's sampling accessories ensure that you can maintain precise temperatures and/or pressures.