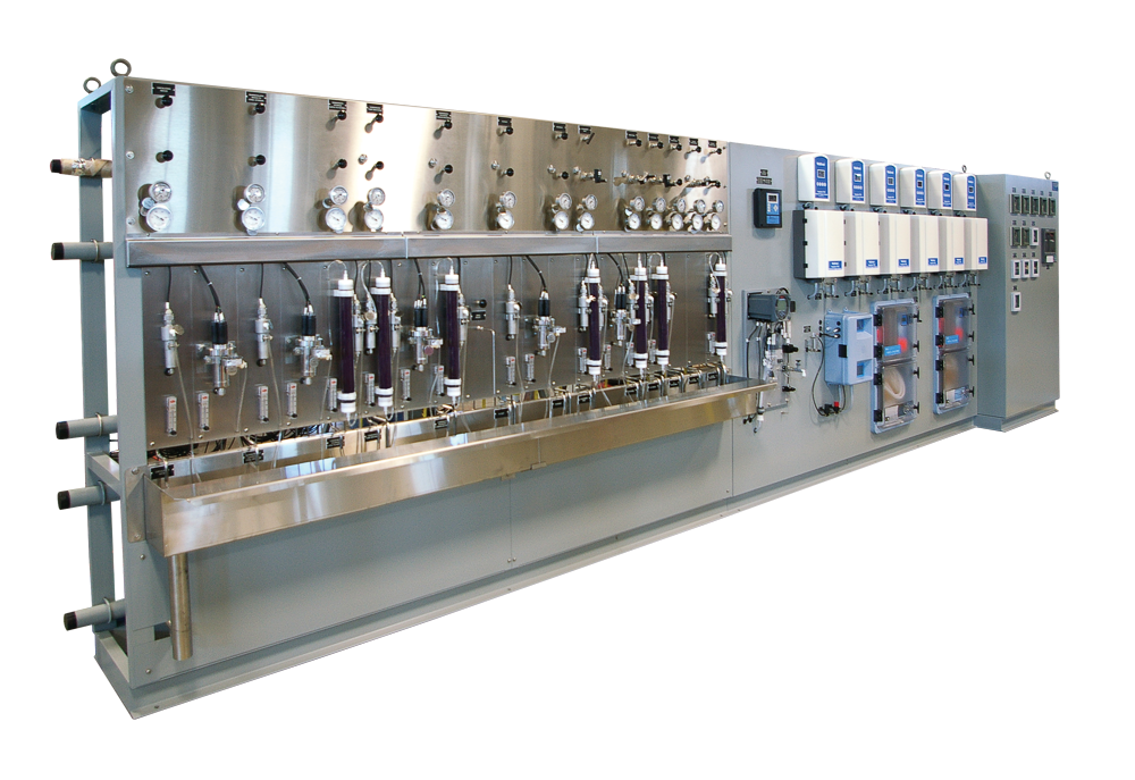
Steam sampling is sometimes viewed as a necessary evil in a process plant. However, the absence of steam due to a boiler shutdown makes for a bad day at a refinery, petrochemical or specialty chemical plant. But one size doesn’t fit all, and a number of variables must be considered to design and implement a practical, reliable steam sampling system.
WHY STEAM SAMPLING?
Steam sampling is a required utility for most chemical, petrochemical and refining processes. Without it, molecules don’t get cracked, reactors don’t get heated, and hopes for high yielding chemical processes don’t materialize.
Steam impurity may cause operational issues with turbines and other process equipment, corrosion of process components, and/or scaling of metal surfaces. To mitigate these risks, analysis of process steam and condensate is an important aspect of any chemical processing or refining operation. In order to achieve accurate analysis, EPRI, ASTM and ASME recommend cooling water samples to 77°F (25°C) to ensure consistent, accurate analysis.
Steam systems must be monitored for expected contaminants, and the level of vigilance must increase as the consequences of failure increase.
THE TOP 5 THINGS TO DO BEFORE IMPLEMENTING A STEAM SAMPLING SYSTEM
1. Get The Right Components
A well-designed sample conditioning system for an individual sample consists of the following components
- Inlet isolation valve
- Blowdown valve (High and/or Low Pressure)
- Primary Sample Cooler and associated inlet and outlet valves
- Primary Cooler relief valve
- Pressure Reducing Valve
- Thermal Shutoff Valve
- Secondary Cooler
- Pressure and Temperature Gauge
- Total Line and Individual Analyzer Flow Indicators
- Back Pressure Regulating Relief Valve
These components are a combination of pressure, temperature, and flow conditioning to ensure a representative sample that is safe for the operator.
2. Understand Steam Sampling Dynamics
A steam sampling system design differs from a gas phase sampling system and from a single-phase liquid sampling system. Steam changes state as its temperature and pressure change and these transitions must be accounted for to avoid inconsistent, non-representative results. As such, you should consider:
- Sample probes: Sample extraction requirements differ when sampling saturated steam versus water (single phase liquid) or superheated steam (free from water droplets at the point of extraction).
- Sample line sizing: The lower the steam pressure, the larger the sample line required to avoid “choking” and loss of representative sample flow.
3. Follow General Design Guidelines
When considering options for installing sample panels and systems, the following must be considered:
- If possible, indoors or inside a temperature-controlled shelter is best
- Outdoor locations are acceptable if some common sense precautions are taken, such as not locating analyzer displays in direct sunlight, providing proper freeze protection, and providing adequate cooling for temperature sensitive electronic or sensor components
- Closer to the sample source is better to minimize transport challenges and sample transit times
- There must be sufficient space to access the analytics and perform maintenance.
4. Ask The Right Questions
You must ask a few key questions to configure a successful system:
- Is my sample pressure > 500 psig or < 500 psig? If greater, a rod-in-tube device such as a variable pressure reducing element (VREL) is required to avoid dissociation of water and to ensure reliability. This device “spreads” the pressure drop across a large surface area vs. taking the drop across a small surface like a needle valve. A needle valve is acceptable for pressure drop for sample pressures <500 psig.
- Is this sample point for grab sample only or am I feeding online analyzers? For high-pressure steam systems, online steam analysis is common. However, in cases where no online analyzer is utilized (low pressure systems), no back pressure regulator is required.
- Should an automatic thermal protection safety device be used in the system? Thermal shutoff valves (TSV) are often applied for steam systems where one of the following applies: 1) Operators interact frequently with this system; 2) Expensive analyzers are part of the system; or 3) The steam sampling system is located in a high traffic area. A TSV automatically shuts off sample flow when samples exceed safe temperatures.
- What cooling sources do I have available at the proposed installation site?
The answer to this question includes corollary questions such as:
- What size sample cooler is required?
- Will it be necessary to utilize a primary and a secondary sample cooler?
- Where must the primary cooler be located to have access to acceptable cooling water?
- What cooling source is available to achieve sample cooling to approximately 77F (25C)?
5. Ensure A Safe Design
The following safety considerations should be considered when designing or utilizing a system:
- A means of sample relief must be provided on each sample line. Combination backpressure regulating/relief valves or variable pressure regulating valves with separate relief valves may be used. A high Cv combination back pressure/relief valve (BPRV) ensures constant sample flow and non-plugging pressure relief function and may eliminate the need for a dedicated pressure relief line.
- Material selection – for cooling water sources derived from city water or otherwise containing high levels of chlorides, Inconel (Alloy 625 or similar) sample tubes are recommended in place of stainless steel to avoid stress corrosion cracking.
- Ensure cooling water lines supplying the primary sample cooler are sized appropriately. Common field errors include use of sample tubing instead of piping for the cooling water service. Sample tubing has a smaller internal area than piping with the same outer diameter (OD). Samples should be routed with tubing, cooling water with piping typically. Insufficient cooling water flow will result in rapid cooler failure.
- Setup sample coolers with isolation valves so they can be drained and to provide pressure relief on the shell side of the cooler in the event of a loss of cooling water incident.
- In addition, note the cooling water flow globe valve is located downstream of the cooler to maintain a backpressure and minimize cavitation and boiling of cooling water in the cooler.
- The isokinetic sample flow required for the sample line usually exceeds the flow required by pure water analytics. For this reason, analyzers should be operated on a branch line and the surplus flow sent to drain or a sample recovery system.
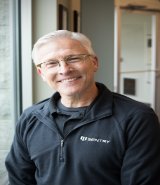
Written by Jeff McKinney
As an industry manager for chemical and petrochemical refining, Jeff is an expert in those markets and is experienced in power generation as well. Jeff is focused on serving these key markets and sharing information on how Sentry sampling and monitoring products and systems can meet any petrochemical or chemical application, anywhere. He is responsible for our market strategy and product offerings, and is alwasy interested in exchanging information on specific industry applications and solutions that meet customer needs.
Related Posts
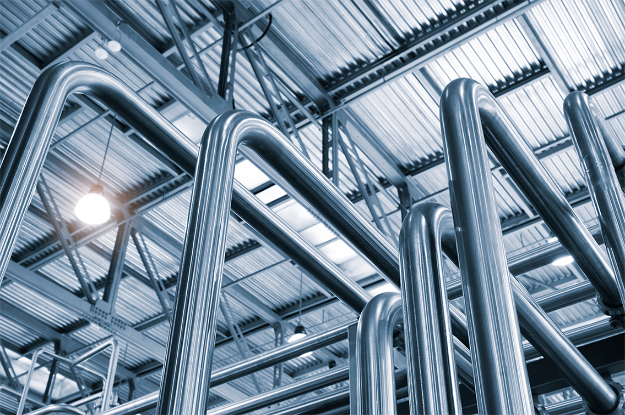
Power Generation
Do You Trust Your Process Analytics?
Accurate sampling all depends on regular maintenance. Are you maintaining the critical instruments that your plant relies on?
Read More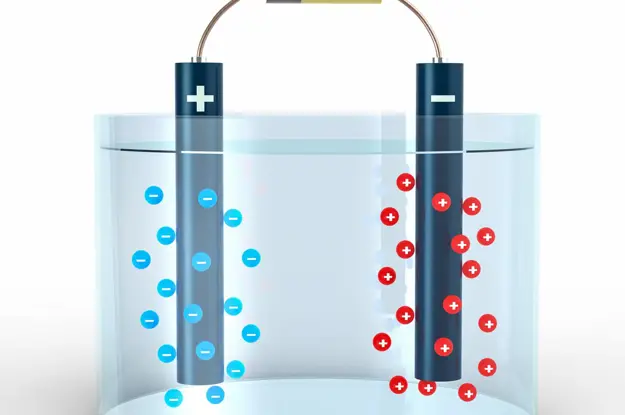
Power Generation
Cation Conductivity vs. Specific Conductivity
Conductivity is useful as a general measure of stream water quality. Each stream has a relatively constant range of conductivity. Once a baseline is established, it can be compared with regular conductivity measures.
Read More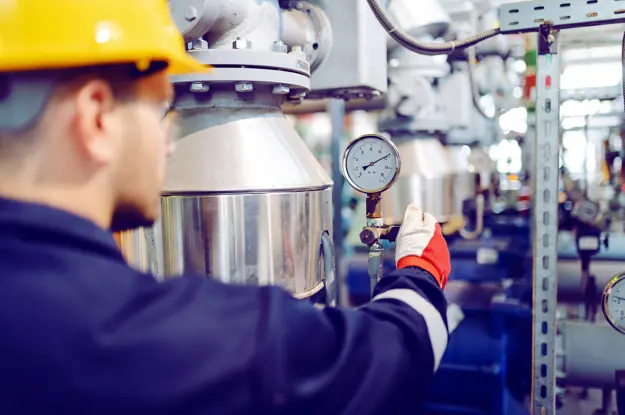
Power Generation
Monitoring Cooling Water Systems to Improve Plant Performance
Many plants within the manufacturing industry include processes where the product stream must be heated, cooled, or both to facilitate production. These plants often use heat exchangers or sample coolers with recirculating cooling water systems to do so.
Read More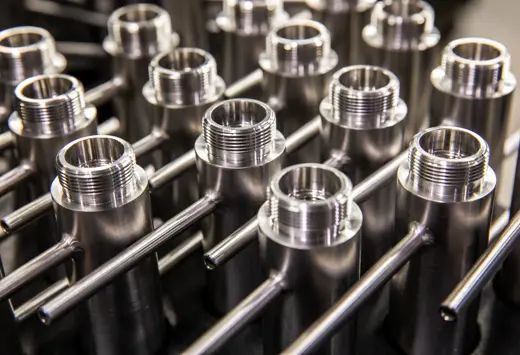
Protect Your SWAS
Sentry's sampling accessories ensure that you can maintain precise temperatures and/or pressures.