Monitoring Cooling Water Systems to Improve Plant Performance
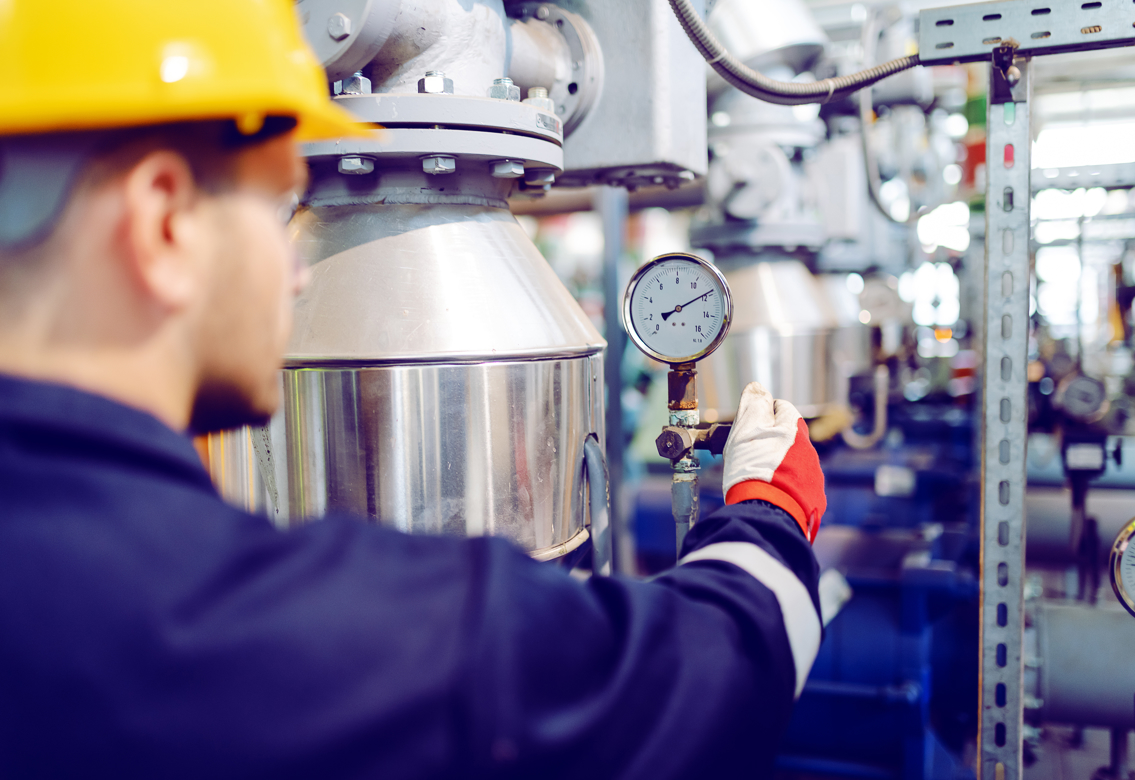
Many plants within the manufacturing industry include processes where the product stream must be heated, cooled, or both to facilitate production. These plants often use heat exchangers or sample coolers with recirculating cooling water systems to do so.
Mineral and bacterial content can be controlled with recirculating water systems within power utilities. Recirculating water systems are designed to provide access to the water and reduce wait time by creating a loop. With this loop, mineral and bacteria content is controlled to avoid fouling or corrosion, which causes equipment damage, increased maintenance costs, inefficient production, and personnel or public health concerns. By monitoring your plant's water purity, you can minimize corrosion and biofouling while maximizing your plant’s output.
Cooling Water Systems
Proper temperature control in your SWAS sample coolers is essential to maintaining safe and representative sampling, however, cooling water touches critical components across your plant, so it is crucial to control this temperature. To do so, many plants cool liquid streams by feeding them through the tubes of shell-and-tube or similar design heat exchangers while cooling water pumps through the exchanger. Cooling water becomes hotter as samples or products’ heat transfers through the tube walls. In turn, the recirculating water needs to be cooled by transferring heat to the atmosphere by a cooling tower or through a direct feed of source water from a river or lake through a large heat exchanger or condenser.
Monitoring Cooling Water Systems
In a recirculating cooling water system cooled by a tower, water volume is lost to evaporation making contaminants cycle up further concentrating dissolved liquids over time. To control this, cooling towers must be blown down from time to time to remove minerals. This is where proper monitoring is needed. Cooling water requires chemical treatment to prevent corrosion, biofouling, or other adverse conditions because a pH excursion or biofouling event can shut down production. The resulting chemistry must be monitored continuously to ensure adequate chemical feeds and proper cooling water conditions.
Benefits of a Cooling Water Analys
is Cooling water analysis panels allow representative samples to be obtained from your cooling water or recirculating water systems and sent to analyzers. These analyzers have the ability to send alarms when certain conditions are met, such as a change in conductivity or pH crossing a threshold where scaling and fouling could become an issue.
Advantages include:
- Maintaining water purity: monitoring water cooling can help maintain proper water chemistry.
- Avoiding unplanned shutdowns: Inefficient cooling towers can lead to costly unexpected shutdowns.
- Improving equipment performance: Reduced cooling capacity due to water purity issues can limit production.
- Reducing safety and environmental risks: Water quality monitoring can include hydrocarbon detection, which warns of malfunctions and allows maintenance to remove hydrocarbons safely and initiate repairs.
Sentry Equipment has deep experience and technical expertise in utility sampling throughout North America, which has made us the go-to partner for complete SWAS health. We can provide panels customized to your requirements to facilitate monitoring and maximize plant performance. Explore our sample cooling solutions. Contact us at +1-262-567-7256 or complete our online contact us form for more information.
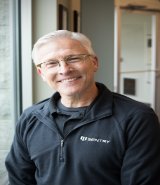
Written by Jeff McKinney
As an industry manager for chemical and petrochemical refining, Jeff is an expert in those markets and is experienced in power generation as well. Jeff is focused on serving these key markets and sharing information on how Sentry sampling and monitoring products and systems can meet any petrochemical or chemical application, anywhere. He is responsible for our market strategy and product offerings, and is alwasy interested in exchanging information on specific industry applications and solutions that meet customer needs.
Related Posts
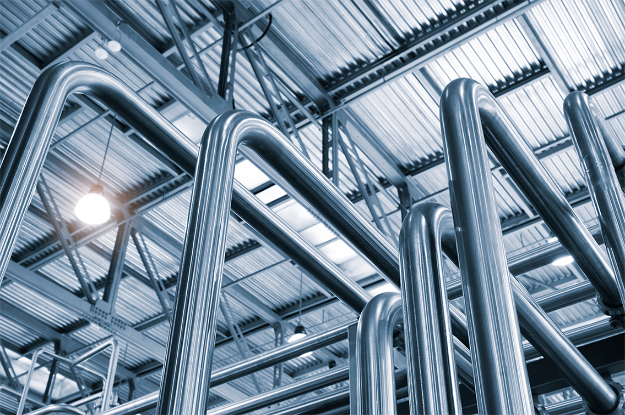
Power Generation
Do You Trust Your Process Analytics?
Accurate sampling all depends on regular maintenance. Are you maintaining the critical instruments that your plant relies on?
Read More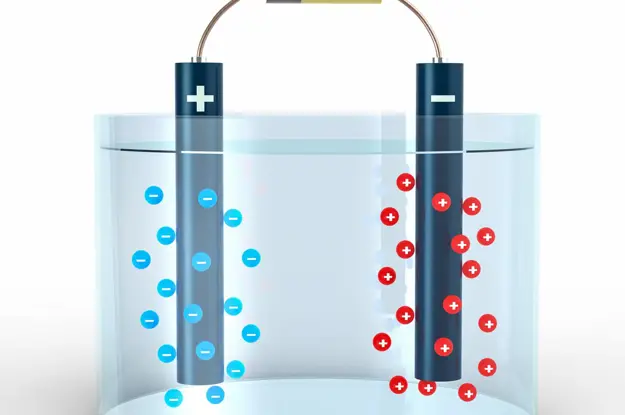
Power Generation
Cation Conductivity vs. Specific Conductivity
Conductivity is useful as a general measure of stream water quality. Each stream has a relatively constant range of conductivity. Once a baseline is established, it can be compared with regular conductivity measures.
Read More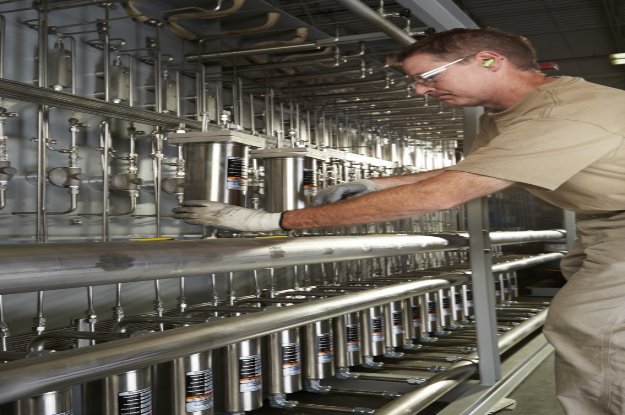
Power Generation
Prepare Your Equipment for the Summer Heat with a Two-Stage Cooling Configuration
Avoiding extreme summer weather and even regular summer weather is not avoidable, and these conditions can cause havoc on steam and water analysis systems (SWAS) without adequate preparation.
Read More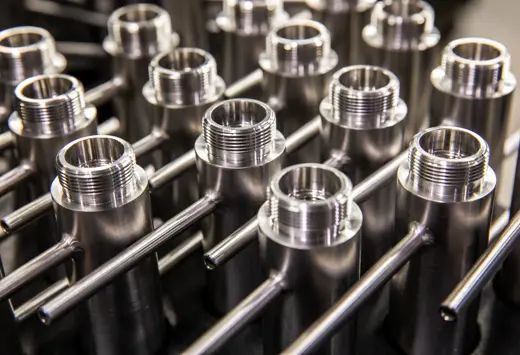
Protect Your SWAS
Sentry's sampling accessories ensure that you can maintain precise temperatures and/or pressures.