Protect Your Equipment with a Coolant Recycling Program
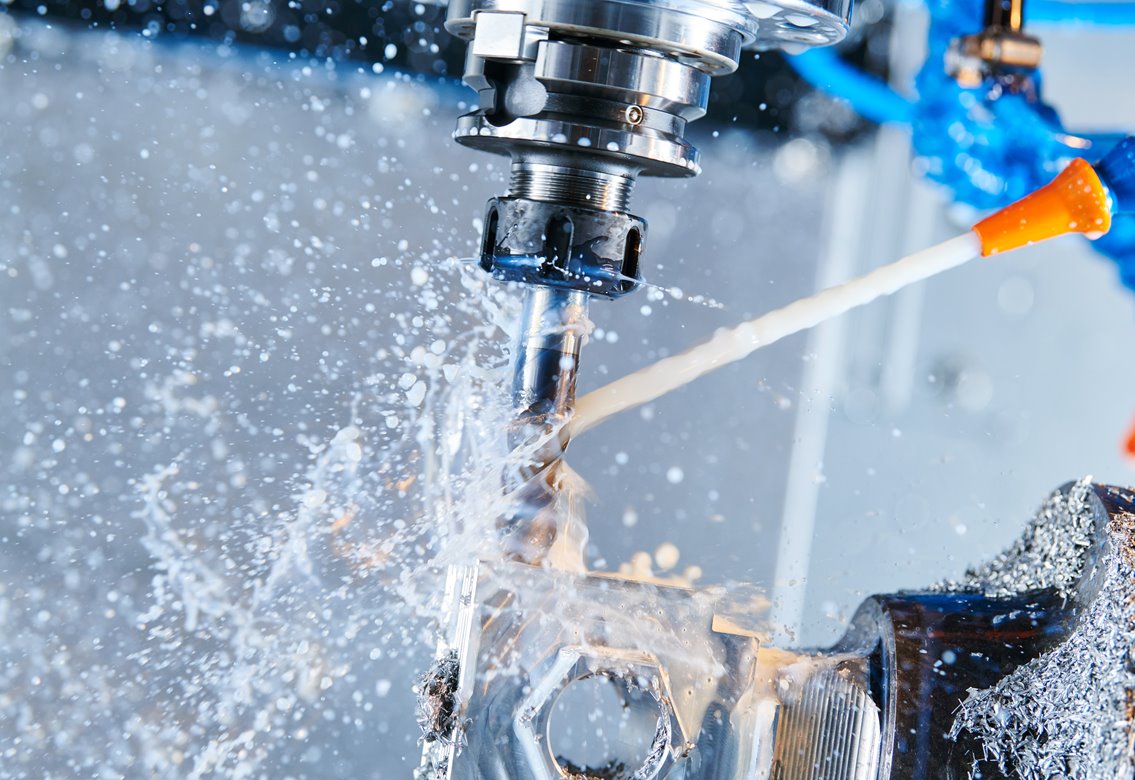
Manufacturing processes are inundated with lubricants and other industrial fluids. Managing these fluids is critical to protecting equipment and ensuring worker safety.
Adding the rising costs of fluid, waste disposal, maintenance, and compliance with workplace safety and environmental regulations, as well as improper fluid management, can significantly impact your bottom line.
In today’s competitive and regulated environment, plants need a smart approach to increasing efficiency, reducing costs, mitigating risks, and protecting equipment investments. A way to solve this is with coolant recycling systems. Through continuous system recirculation, coolant recycling systems clean and reuse fluids to efficiently safeguard your manufacturing equipment and reduce costs.
The basics of Coolant Recycling
Coolant recycling systems regularly remove contamination, such as tramp oils, solids, and bacteria, from machining and grinding fluids so these clean fluids can be safely and efficiently reused in equipment.
The Coolant Recycling Process
- Dirty fluid flows into the system by a sump sucker, drum vac, or a manual process.
- Large debris and particles are captured by an inlet filter, typically a 100-micron reusable bag.
- After removing large debris, a floating suction skimmer directs surface fluid through an oil and water separator to remove free and mechanically dispersed tramp oils.
- The clean treated fluid flows by gravity from the separator into a clean tank and then overflows continuously back into the inlet tank, which provides multi-pass filtration as well as recirculation and aeration.
- A polishing filter loop with a magnetic filter (if ferrous fines are present) and bag filters provide filtration to 5-10 microns. Finally, cleaned coolant can be supplied back into your operations.
- The ozone generator effectively kills bacteria and odors from the environment.
- A water and proportionator system is incorporated into the system to top off with new coolant as needed to keep the system filled.
Benefits of Coolant Recycling
Implementing a reliable coolant recycling system can help you:
- Reduce fluid purchases by 35% to 65%
- Reduce waste disposal costs by up to 90%
- Eliminate environmental risks and the liability of off-site disposal
- Extend the life of tooling, pumps, and other valuable production equipment
- Decrease equipment downtime to increase overall productivity and efficiency
- Enhance the work environment and worker safety by removing contaminants from fluids
- Reduce the man-hours spent managing coolants
How to Implement a Coolant Recycling System
First, identify the issues pertaining to your coolant maintenance, usage & waste expenditures. At Sentry Equipment, we have a specialized team who can visit your facility to help you with this process and troubleshoot issues with your team.
Next, it’s essential to assess what type and capacity of coolant recycling you need. For example, Sentry’s SmartSkim CoolantLoop Recycling Systems come in various scalable sizes for many operations. To select your correct size, identify the available space and coolant needed to recycle. Other factors include the amount and size of sumps and disposal costs.
Finally, it’s time to install the coolant recycling system and other necessary components (such as a sump cleaner) to clean fluids quickly and efficiently.
Choose a Trusted Partner in Coolant Recycling
With more than 100 years of experience, Sentry Equipment can provide coolant recycling systems to help minimize chemical and waste costs and maximize safety while extending the life of your equipment. Plus, our components improve efficiencies and systems regardless of brand or manufacturer. Our systems are backed by technical and sales experts, safeguarding your equipment now and in the future.

Written by Sentry Equipment
With proven sampling expertise since 1924, Sentry products and services provide business operations the critical insights to optimize process control and product quality. We deliver true representative sampling and analysis techniques to customers around the globe, empowering them to accurately monitor and measure processes for improved production efficiency, output and safety. Standing behind our commitments, we are determined to tackle any application, anywhere.
Related Posts

Oil Separation/Coolant Recycling
CASE STUDY: How to Increase the Efficiency of your Facility with Used Equipment
Read More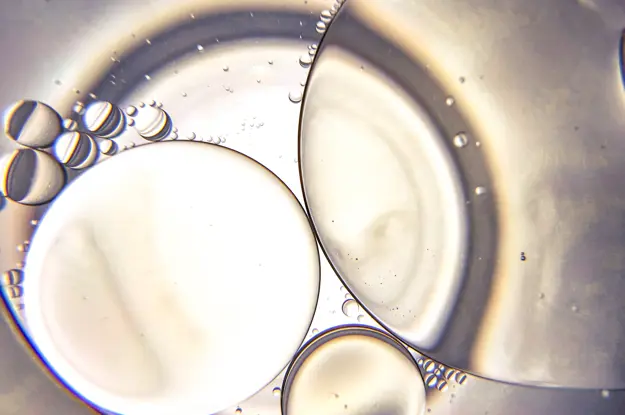
Oil Separation/Coolant Recycling
How to Increase the Efficiency and Output of Your Evaporator
As EPA (Environmental Protection Agency) expands regulations and enforcement on the discharge and disposal of industrial fluids from metalworking and metal-finished plants, we can see more equipment being purchased to treat and or solve tSmartSkim Recycling & Filtrationhe problem of waste.
Read More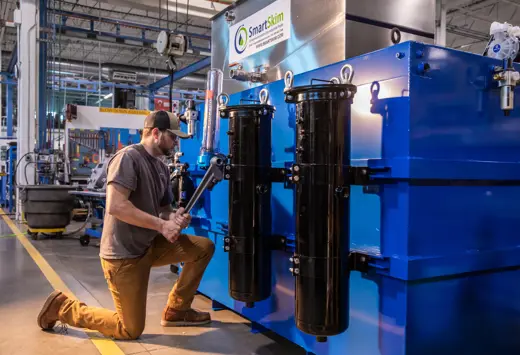
Maximize Manufacturing Processes
Sentry's SmartSkim product line can help maximize your manufacturing processes with coolant recycling and oil separation technology.