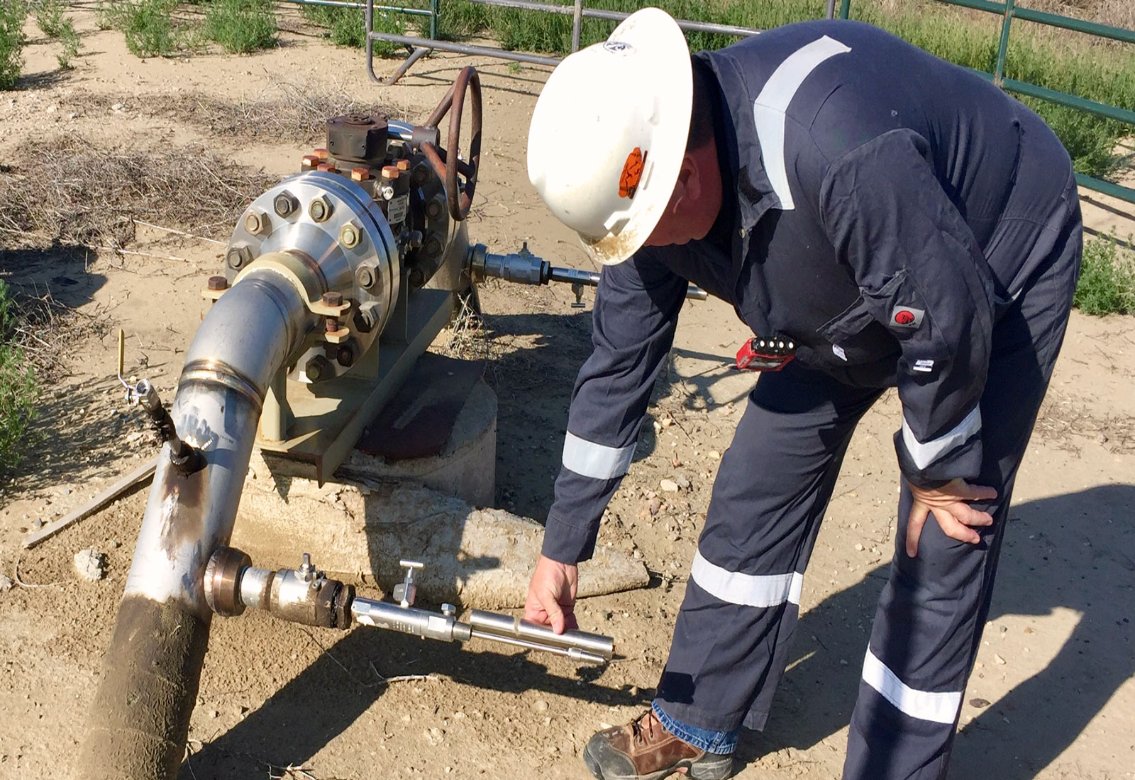
Internal corrosion monitoring is critical to preventing and addressing corrosion inside gas and oil pipelines. It is also the first step in choosing the right corrosion mitigation method based on identified corrosive constituents.
Most hydrocarbon facilities implement internal corrosion monitoring methods to identify, protect against and eliminate corrosive contaminants, including hydrogen sulfide (H2S), carbon dioxide (CO2), oxygen (O2), water (H2O) and microbial organisms. These monitoring methods can help operators ensure the integrity of oil and gas field pipelines that are essential for uninterrupted production.
Corrosion monitoring can also give operators the real-time, continuous and periodic data they need to choose the right corrosion mitigation method, based on the quantification and qualification of the corrosive constituents identified by the internal corrosion monitoring system.
3 KEY CORROSION MITIGATION METHODS
Pipelines used for hydrocarbon production, gathering, transportation, storage and distribution must be designed to allow for corrosion mitigation with one or more of the following generally accepted methods:
1. Pigging
Pigging pipelines is the most commonly used method for cleaning pipelines to eliminate corrosive materials and ensure the line is running smoothly. In this process, the pigs are introduced into the line via a launcher and removed at the pig trap or receiver. The pig is pushed through the line by the process fluid or towed by another device or cable. Pigs scrape the sides of the pipeline and push debris ahead, preventing buildup.
2. Siphons
Many hydrocarbon gas facilities use siphons to remove corrosive liquids from pipelines and vessels preventing the development of corrosion.
In pipelines, these siphons are often required for low areas in the lines, where a pig can’t clear the liquids. A siphon needs to reach great depths and usually requires a “hot tap” – a new pipeline connection point without shutting down the pipeline – to set the access the point.
3. Chemical Mitigation
Chemical treatment is the primary solution for most internal pipeline corrosion problems. Once the corrosive agent is known, the company can assess its options for implementing a chemical mitigation program.
Prior to beginning a chemical mitigation program, the corrosive constituent must be identified and quantified. That’s because corrosion inhibitors and scavengers can be tailored to address fluid phases, operating conditions, expected flow rates and product chemical variations. Inhibitor distribution systems should be carefully monitored and maintained for an optimized chemical treatment program. This system should always be capable of reliably dispersing and distributing accurate dosages.
CHEMICAL TREATMENT DISPERSION AND DISTRIBUTION METHODS
- Injection atomizers use a process that involves forcing the chemical into a fine mist which, when done correctly, causes the liquid to mimic the gas process. It’s required for chemical scavengers when applied to a gas process.
- A mixing probe injects dense liquids into a gas stream and injects liquids into a liquid stream. This method is proven to be a better method than a quill for complete dispersion and distribution.
- Quills should only be used when injecting liquids into a liquid process. Results are inconsistent when injecting liquids into a gas stream with velocities < 15 feet/second.
- Contact Vessel - Natural gas is diverted through a vessel filled with a scavenging fluid such as amine or triazine. Dry bed adsorbent contractors are also an option with certain restrictions.
- Chemical batching utilizes a pig to apply chemicals, such as corrosion inhibitors and biocides, along the pipe walls.
OPTIMIZE YOUR CHEMICAL MITIGATION PROGRAM
- Choose the right injection site – In many pipelines, there’s a shortage of long, straight, obstruction-free runs of pipe. Operators should carefully consider injection sites based on the locations of pipe elbows and obstructions such as valves, regulators, and orifice plates which will separate the liquid from the gas.
- Keep the end goal in sight – Proper dispersion and distribution of the injected chemical is critical for thoroughly treating the entire pipeline. In a gas process system, complete and thorough atomization is a must.
- Injection maintenance – It’s important to remember that injection atomizers, mixing probes and quills require regular maintenance. Retractable models ensure proper maintenance is carried out on a regular basis.
- Automate and monitor – Chemical injection and contact vessels should be automated and remotely monitored for optimum performance.
- Don’t use too many chemicals – Overexposing the most popular chemical scavengers to corrosive constituents creates solids, which can cause additional problems within pipelines.
- Balance your methods – A balanced corrosion mitigation program includes both pigging and chemical applications, so it’s important to consider using each method where it’s most appropriate.
Regardless of the choice of method, properly mitigating internal corrosion as it arises is crucial to proper pipeline maintenance and performance. These timely choices will keep your equipment running longer and reduce future downtime and repair costs.
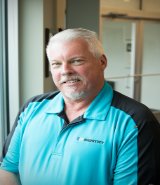
Written by Lance Witt
With over 25 years in the hydrocarbon industry, Lance Witt brings an unique perspective to Sentry Equipment as the Regional Sales Manager. He is a wealth of industry knowledge as an author and presenter fpr ASGMT, ISHM, AFMSC and Gas Well Deliquification Workshops. He is also a technological expert with 3 patents on chemical optimization and an active NACE member.
Related Posts
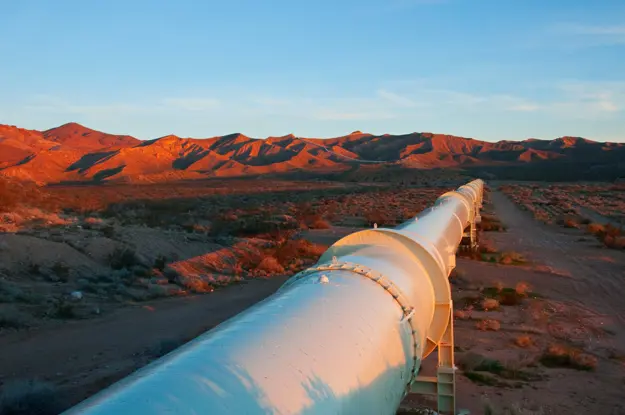
Corrosion
PHMSA Mega Rule: Your Guide to Navigating the New Regulations
The pipeline Industry has heard a lot about the Pipleine and Hazardouse Materials Safety Administrations (PHMSA) three rules to reduce the frequency of pipeline failures. Now, the third and final rule has been released.
Read More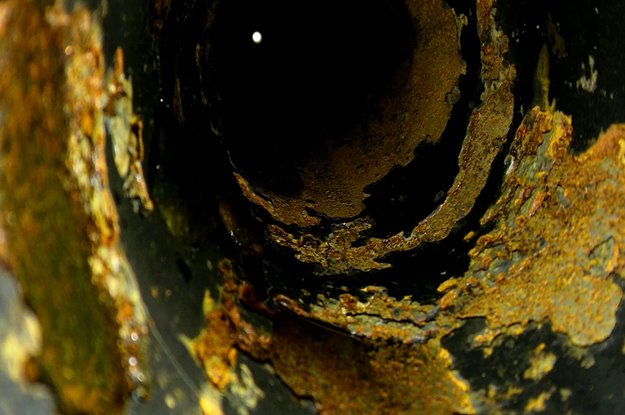
Corrosion
Internal Corrosion Monitoring: What You Need to Know
Pipelines carrying oil and gas experience internal corrosion when water is present inside the lines.
Read More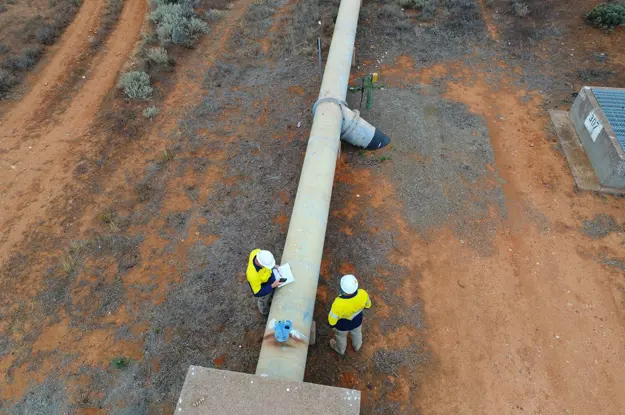
Corrosion
What are Atomizers and Do I Need Them?
Corrosion is a significant contributor to gas and oil pipeline failures. That is why many oil and gas companies implement chemical treatment methods to eliminate corrosive contaminants within gas pipelines. But chemical efficiency can be drastically affected by improper injection methods.
Read More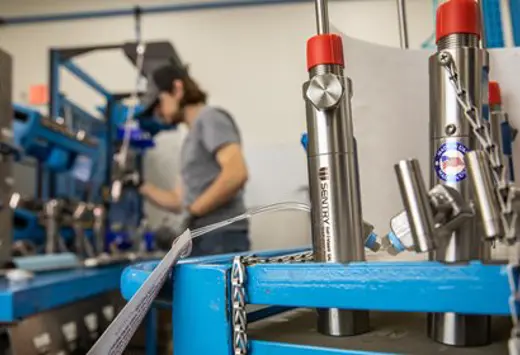
Mitigate Pipeline Corrosion
Sentry's complete line of corrosion protection products will maximize your pipeline's longevity.